«Сибур» получил свою технологию производства компонентов для полиэтилена
Собственная разработка оказалась эффективнее зарубежных аналогов
«Сибур» завершил испытания пилотной установки по производству одного из соединений для достраиваемого компанией комплекса «Запсибнефтехим», сообщил «Ведомостям» представитель нефтехимического холдинга. Речь о выпуске альфа-олефинов по собственной технологии, рассказал он. Указывать точное название соединения в компании не стали, сославшись на коммерческую тайну.
Решение о строительстве промышленной установки на новом комплексе в Тобольске может быть принято в 2020 г. «Если примем решение в 2020 г., то запустить сможем уже в 2022 г.», – говорит представитель компании. Стоимость такого проекта, по оценкам «Сибура», может составить «несколько миллиардов рублей».
Альфа-олефины (сомономеры) – один из элементов в процессе получения полиэтилена (1,5 млн т – «Запсибнефтехим»). Достроить комплекс «Сибур» планирует в первом полугодии 2019 г. В базовом сценарии необходимые для производства в Тобольске альфа-олефины «Сибур» предполагает импортировать.
Однако испытания опытной установки (стоимость более 600 млн руб., была построена в научном центре «Сибура» в Томске. – «Ведомости») показали, что при росте собственного потребления сомономера строительство промышленного образца на «Запсибнефтехиме» может оказаться экономически оправданным, рассказал директор корпоративных НИОКР «Сибура» Дмитрий Степкин. «По сути, альфа-олефин, о котором идет речь, производится из сырья и так используемого на «Запсибнефтехиме». Собственное производство снижает затраты на него по сравнению с импортом. Вопрос только в масштабе такого производства. Оно должно окупить инвестиции на разработку технологии и строительство промышленной установки с учетом альтернативной стоимости денег и ресурсов – будем считать», – говорит Степкин.
Одним из определяющих факторов может стать окончательное инвестиционное решение по строительству Амурского газохимического комплекса (АГХК). Оно может быть принято во второй половине 2019 г. «Мы сможем еще раз посчитать экономику и принять решение», – рассказывал в интервью «Ведомостям» председатель правления компании Дмитрий Конов. АГХК (проектная мощность – 1,5 млн т полиэтилена в год) может оказать существенное влияние на загрузку перспективной мощности [установки по производству сомономеров], объясняет последовательность решений представитель «Сибура». Кроме того, в случае строительства промышленной установки компания рассчитывает экспортировать часть продукции и конкурировать с зарубежными производителями как минимум в пределах СНГ, где логистика доставки может стать серьезным конкурентным преимуществом, добавляет он.
Экономический эффект от строительства собственной установки теоретически может окупить затраты на ее строительство за несколько лет, говорит руководитель центра Rupec Андрей Костин. В среднем на полиэтилен премиальных марок приходится лишь 20–35% от общей мощности производства, а доля сомономера в таком продукте не выше 7%, указывает он. «Импорт одной тонны бутена-1 (самый простой из альфа-олефинов. – «Ведомости») сейчас обходится в сумму около $1800. Если экономия за счет собственного производства составит хотя бы треть, при полной загрузке «Запсибнефтехима» с АГХК «Сибур» сможет выигрывать около $44 млн в год», – посчитал Костин. Бутен – самый дешевый в линейке сомономеров, если речь идет о более сложном соединении, инвестиции «Сибура» могут окупиться еще быстрее, уточняет эксперт.
Идея о разработке собственной технологии получения альфа-олефинов возникла у «Сибура» еще в 2009 г. Альтернативой могло бы стать строительство на «Запсибнефтехиме» установки по зарубежной технологии. Но ею на тот момент владела лишь одна компания, предпочитавшая экспортировать готовый продукт. После перехода от лабораторных испытаний «в пробирке» к постепенному увеличению масштаба опытного производства интерес к покупке лицензии снижался у самого «Сибура», рассказывает руководитель направления по оптимизации технологических процессов Владимир Бушков. С точки зрения капитальных затрат на строительство собственная разработка оказалась гораздо экономичнее, добавляет он.
«Затраты на производство продукта по нашей технологии сравнимы с зарубежными аналогами, но условия процесса мягче – ниже температура и необходимое давление», – объясняет Бушков. Это снижает требования к основному оборудованию и, соответственно, его стоимость. Вместе с возможностью уйти от валютной составляющей это существенно снижает затраты на строительство, добавляет он.
Особенности технического решения могут сделать разработку привлекательной на рынке лицензирования, рассчитывают в «Сибуре».
Стоимость лицензии, хотя она и может исчисляться в миллионах долларов, сама по себе невысока, обращает внимание Костин. «Прибыльным этот бизнес становится, когда лицензиар продает ее в пакете с услугами по инжинирингу и ведению проекта. У «Сибура» есть такие возможности, но все равно ожидать очереди желающих купить лицензию не стоит, – считает Костин. – Проектов большой мощности по линейному полиэтилену вроде «Запсибнефтехима» и АГХК, что оправдало бы лицензирование, сейчас немного. За них придется конкурировать». Найти рынок для экспорта чуть проще, продолжает эксперт. «У Казахстана, Узбекистана и Азербайджана есть планы по строительству своего производства полиэтилена. «Сибур» вполне может побороться за них как за рынки сбыта. Но в дальнем зарубежье – сомнительно. Там основной поставщик сейчас Саудовская Аравия, бороться с ней может быть сложно», – говорит Костин.
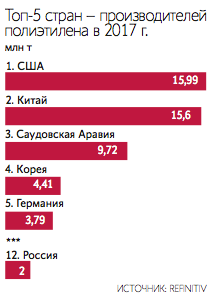