Искусство маленьких улучшений: три кейса роста производительности
Как федеральная программа помогла свиноводам, энергетикам и производителям майонеза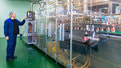
Когда кажется, что возможности для роста исчерпаны, бывает достаточно опытного взгляда извне, чтобы понять, как много ресурсов для снижения издержек и роста производительности есть у самого бизнеса. Искусство маленьких шагов, бережливое производство и постоянные вопросы, как можно сделать каждое действие еще эффективнее, приносят ощутимые результаты, убеждаются участники нацпроекта «Производительность труда и поддержка занятости».
«Ведомости&» собрали несколько примеров улучшений, которые позволили сократить время производства, победить переработки и бесцельные простои – и в конечном итоге найти новые возможности для роста бизнеса.
+30% к производительности за два месяца
Один из крупнейших свиноводческих комплексов Тюменской области – ООО «Согласие» (70 000 голов) стало участником нацпроекта «Производительность труда и поддержка занятости» в марте 2019 г. Компания понимала: процессы можно совершенствовать, но как именно, было не ясно. «Хотелось что-то менять, улучшать, а четкого понимания как было мало. Для меня лично это [участие в нацпроекте] получение дополнительного управленческого опыта», – объяснила «Ведомости&» заместитель начальника мясокомбината свинокомплекса «Согласие» Виктория Парфенова. В проекте повышения производительности труда она стала руководителем рабочей группы.
«Согласие»
сокращение времени протекания процесса с 9 часов 35 минут до 6 часов 43 минут. Фактическое сокращение времени на 30%;
сокращение запасов сырья в потоке с 470 до 70 кг в смену. Фактическое изменение в 6,7 раза;
повышение производительности труда (выработки) в потоке с 12 789 кг/чел. в месяц до 19 404 кг/чел. в месяц. Увеличение производительности на 52%;
повышение производительности труда (выработки) грузчиков в потоке с 16 528 кг/чел. в месяц до 28 750 кг/чел. в месяц и дополнительно ведение учета в программе. Увеличение производительности на 73%.
«Согласие» – региональный производитель свинины. Предприятие полного цикла производит более 30 т продуктов в сутки, в каталоге компании – около 180. Для работы в рамках нацпроекта рабочая группа выбрала сырьевой участок предприятия – из-за него часто простаивали колбасный и маринадный цеха.
Эксперты Федерального центра компетенций в сфере производительности труда (ФЦК) проанализировали работу «Согласия» и обнаружили: основной «ценной» работе (которая создает добавленную стоимость продукта) сотрудники уделяют 35% рабочего времени. Остальные 65% времени занимают необходимые, но не ценные действия. Грузчики много перемещались в поисках средств транспортировки, сырья и продукции, а также необоснованно дополнительно транспортировали продукцию на всех этапах производства, что в совокупности занимало более 8 часов в день на всех. В результате грузчиков не хватало, а спланировать их работу и отдых на месяц вперед было сложно. Переработка на одного грузчика в компании составляла 15–20 часов в месяц, т. е. 120 000–150 000 руб. доплат за переработки на всех. Сотрудники часто брали больничные и были в целом недовольны.
На пилотном сырьевом участке эксперты ФЦК порекомендовали перераспределить обязанности и зоны ответственности среди грузчиков. Оказалось, что вместо 27 человек с работами могут справиться 24, а остальных направили на сбор заявок и отгрузку товара. Всех грузчиков обучили пользоваться системой «1С Склад», что позволило высвободить трех кладовщиков. После изменений исчезли переработки, сократилось число больничных, горизонт планирования работы грузчиков вырос до месяца. Сотрудники стали уходить домой вовремя.
Оптимизировали и работу обвальщиков: кроме обвалки они срезали туши и укладывали их на стол – на это уходило время. После консультаций из процесса исключили лишние перемещения и ожидания из-за завалов продукции. Рабочие столы были выстроены в поток, работа начала вестись по «времени такта» (чтобы у каждого обвальщика операция занимала одинаковое время, необходимое для следующего передела). В результате перебалансировки производительность труда на одного обвальщика выросла на 61%, а процесс стал проходить почти в 2 раза быстрее. Количество разделанных туш за смену выросло со 170 до 243. Улучшился еще один из ключевых показателей: количество сырья, находящегося в обработке, сократилось на 60%.
При внедрении улучшений эксперты ФЦК использовали стандартные инструменты бережливого производства: составили карту процессов потока, организовали удобные рабочие места по методу 5С (сортировка, соблюдение порядка, содержание в чистоте, стандартизация, совершенствование), составили регламенты выполнения работ, создали доску решения проблем и инфоцентр для отслеживания оперативной информации для персонала. Высвободившихся сотрудников компания направила в другой цех: теперь они разделывают дополнительные 13 000 кг тушек курицы в месяц (и эта цифра растет). Внедрение всех этих улучшений заняло два месяца. «Производственный процесс на оптимизируемых участках стал прозрачным, а сотрудникам стало легче выполнять свои обязанности. Нам, как руководителям, стало легче управлять», – говорит Парфенова.
Экономический эффект от внедрения изменений составил, по оценке компании, 14,45 млн руб. в год (выручка предприятия – 2,4 млрд руб. в год). Половину от этой суммы, 7,57 млн руб., предприятие получило от перераспределения высвободившегося персонала на другие производства.
Теперь на предприятии совершенствуют работу и на других участках. «Уже оптимизирована работа пельменного цеха, внедрены сопутствующие улучшения на складах готовой продукции по системе 5С, сокращен процесс отгрузки продукции с 2 часов до 40 минут. Сейчас одновременно совершенствуются подразделения колбасного цеха, кормоцеха, автогаража. Составлен плотный план реализации проектов на 2020 г.», – рассказала Парфенова, добавив, что экономический эффект этих улучшений еще не подсчитан.
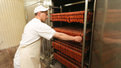
Алтайский кайдзен
Барнаульский производитель паровых котлов и энергетического оборудования «Межрегионэнергосервис» (ПО «МЭС») задумался об эффективности, когда стало очевидно, что вскоре объем заказов может существенно вырасти. «Главные наши клиенты – предприятия энергетической отрасли. В ближайшие годы в российской энергетике планируется масштабная модернизация оборудования. Для нас это может означать рост заказов. Поэтому мы решили, что пришло время менять существующий подход к организации производства, развивать квалификацию персонала», – рассказывает руководитель проектов ООО «Производственное объединение «Межрегионэнергосервис» Роман Омельченко. МЭС выпускает и устанавливает паровые котлы и энергетические системы для ТЭЦ. На предприятии работает 450 человек.
«Межрегионэнергосервис»
сокращение времени протекания процесса с 59 до 21 дня на один коллектор;
сокращение запасов в потоке с 11 до 6 шт.;
повышение производительности труда (выработки) в потоке с 0,0169 до 0,0472 шт. в смену на человека.
Весной 2019 г. компания присоединилась к нацпроекту «Производительность труда и поддержка занятости». Для достижения целей национального проекта перед компанией стояла амбициозная цель за год увеличить производительность труда на 10%, за два года – на 15% и по итогам третьего года – на 30%. В качестве пилотного направления выбрали выпуск коллекторов. Их производство одно из самых дорогостоящих, оно взаимодействует со всеми цехами и участками предприятия и приносит ПО «МЭС» около 16% выручки (финансовые показатели компания не раскрывает). Направление коллекторов было наименее стабильным: из-за перебоев с поставками сырья и задержек на других этапах сроки производства коллекторов котла для ТЭЦ могли доходить до 59 дней – от момента поставки сырья до отгрузки готового изделия.
Проектная команда из сотрудников МЭС и экспертов ФЦК подробно изучила рабочие процессы, замерила хронометраж изготовления каждой детали, составила карты процессов и предложила несколько качественных изменений, не требовавших инвестиций в производство. Начали со склада: все сырье и комплектующие промаркировали, внедрили систему адресного хранения (запчасти для каждого проекта хранятся отдельно), создали график использования запчастей и небольшой управляемый запас материалов на участке сборки коллекторов. «Если раньше сварщик должен был идти на склад, подбирать там комплектующие и только после этого работать над изделием, то теперь появился комплектовщик, который обеспечивает сварщиков и слесарей в нужное время всем необходимым для работы. Это позволяет сэкономить до 60 минут рабочего времени за смену», – объясняет руководитель проектов МЭС.
Затем проектная группа прошлась по другим процессам: внедрили систему обхода и осмотра оборудования, разработали систему реагирования на аварийные ситуации, создали постоянный резерв расходников для обслуживания оборудования, освободили место в производственных цехах, убрав неиспользуемое оборудование. Результат получился впечатляющим, считает Омельченко: время аварийных ремонтов сократилось с двух суток практически до нуля, на проверку качества сырья (коллекторы должны выдерживать 500 градусов и до 200 атмосфер) завод стал тратить 3 часа против трех восьмичасовых смен – за счет внедрения регламента.
В чистом итоге время производства коллекторов сократилось с почти двух месяцев до 21 дня, роста производительности труда на 10% компания достигла уже к сентябрю. «Теперь мы можем предложить более конкурентные сроки изготовления, что позволит более уверенно выходить на рынок. И это только начало. Мы будем внедрять принципы бережливого производства на всех участках, обучать рабочих и инженеров новому подходу. Мы смотрим на организацию рабочих мест, на эффективность использования рабочего пространства в цехах, стандартизируем рабочие процессы. Впереди путь маленьких шагов и улучшений», – рассказывает Омельченко.
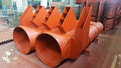
+ 1,6 т соуса на человека в месяц
Стагнация на рынке майонеза и рост в категории соусов подтолкнули Нижегородский масло-жировой комбинат (НМЖК) к поиску новых решений для развития бизнеса. «В условиях острой конкуренции на потребительском рынке повышение эффективности компании – это жизненная необходимость», – объяснил индустриальный директор ГК «НМЖК» Сергей Бобровский. Чтобы сделать это без дополнительных инвестиций, НМЖК вступил в нацпроект и пригласил экспертов ФЦК. За предприятием закрепили двух руководителей проекта от ФЦК, которые первые три месяца присутствовали на предприятии ежедневно.
НМЖК – один из крупнейших в России производителей жиров и маргаринов для пищевой промышленности. У компании восемь заготовительных и два маслоэкстракционных предприятия, а также перерабатывающий завод в Нижнем Новгороде. Главные потребительские марки холдинга – майонезы «Ряба» и «Сдобри», соусы Astoria и маргарины «Хозяюшка».
Нижегородский масло-жировой комбинат
сокращение времени протекания процесса с 1055 до 890 минут;
повышение производительности труда (выработки) в потоке с 9,7 до 11,2 т/мес. на человека;
время мойки оборудования при переходе с одного продукта на другой с 705 до 540 минут.
Предприятие с ФЦК пилотный проект провели на линии соусов Astoria. Их доля в выручке холдинга – около 9%, но хлопот они доставляли больше, чем майонез. Ассортимент соусов в портфеле шире, их выпускают меньшими партиями. На обязательную мойку технологической линии после одного продукта требовалось почти 12 часов (в результате проведенной работы это время сократилось до 9 часов), а это причина 50–60% простоев линии.
Эксперты ФЦК проанализировали процессы производства и предложили несколько эффективных решений. Например, мойку производственной линии рекомендовали начинать раньше, не дожидаясь окончания всех процессов. Дело в том, что дозировочное отделение и фасовка расположены на разных этажах. Первое заканчивает работу на несколько часов раньше, поэтому мыть это отделение можно, пока продолжается упаковка продукта. Чтобы персонал не простаивал без дела, разборку оборудования от наладчика передали дозировщику. А чтобы сотрудники не ходили за средствами индивидуальной защиты и инвентарем с одного этажа на другой, рядом с рабочими местами на линии создали места для хранения инвентаря.

Стандартизация всех процессов и отказ от ручного труда при заклейке коробок (компания установила автоматический заклейщик коробов) позволили высвободить двух из семи операторов в каждой смене (всего в сутках две смены). За счет маленьких улучшений процессов и установки ручек и петель на крышки фасовочного автомата удалось сократить время смены рулона пленки, из которой делают упаковку (причина 8–9% простоев линии), с 11,5 до 10 минут, а время технического обслуживания (3–4% простоя) – с 24 до 20 минут.
Как результат, общее время производственных процессов на пилотной линии фасовки соусов (с учетом мойки) удалось сократить почти на 3 часа до 14 часов 50 минут. НМЖК рассчитывает, что загрузка двух линий на это время может принести около 2,4 млн руб. дополнительной прибыли в месяц (еще 370 000 руб. добавится за счет сокращения времени техобслуживания и смены рулона). За счет уменьшения числа работников на линии производительность труда в потоке выросла с 9,7 до 11,3 т продукта на человека в месяц.
«Проект ФЦК позволил сократить потери на конкретном участке и стал образцовым проектом, на основе которого мы будем улучшать производительность и на других участках и площадках», – рассказал Бобровский. Компания уже своими силами запустила похожие проекты на Урюпинском и Сорочинском маслоэкстракционных заводах. «Следующим шагом стал старт интегрированного проекта «Бережливое производство», который охватит всю цепочку – от поставки сырья, производства и отгрузки клиенту до полки супермаркета», – надеется он. &